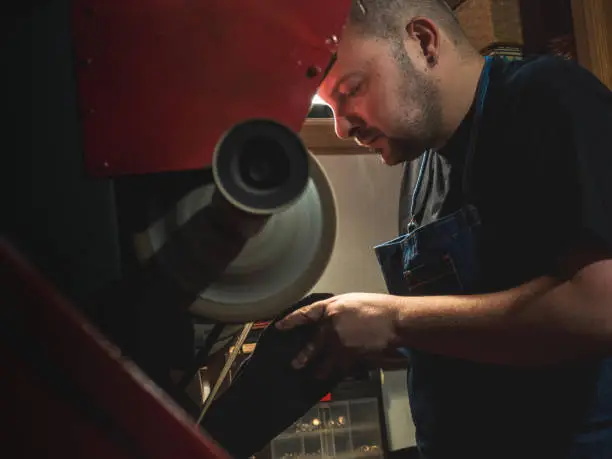

The Cost-Effectiveness of Metal Spinning for Large-Scale Production
Metal forming is a manufacturing process which shapes metal into functional components. Metal spinning is a specific type of metal forming that stands out as a cost-effective and highly efficient method. Industries, including aerospace, automotive, medical, and lighting, use spinning to produce high-quality, symmetrical parts with minimal material waste.
While other metal forming processes, such as stamping, casting, and machining, offer their own advantages, metal spinning is uniquely suited for large-scale production where cost efficiency, durability, and flexibility are paramount.
This article explores why metal spinning is one of the most economical choices for manufacturing, focusing on its advantages in terms of material efficiency, tooling costs, production speed, and long-term durability.
Why Metal Spinning is an Efficient Manufacturing Process
Metal spinning, also known as spin forming, transforms flat sheets or pre-formed metal blanks into complex, symmetrical components. Engineers achieve this by rotating the metal at high speeds on a lathe while applying force with rollers or specialised tools to shape it against a mandrel. The process is particularly suited to producing high-strength, lightweight parts with minimal material waste.
Metal spinning achieves complex geometries without the need for expensive moulds or dies, which translates to significant cost savings, particularly for manufacturers who need flexibility in production runs and rapid prototyping capabilities.
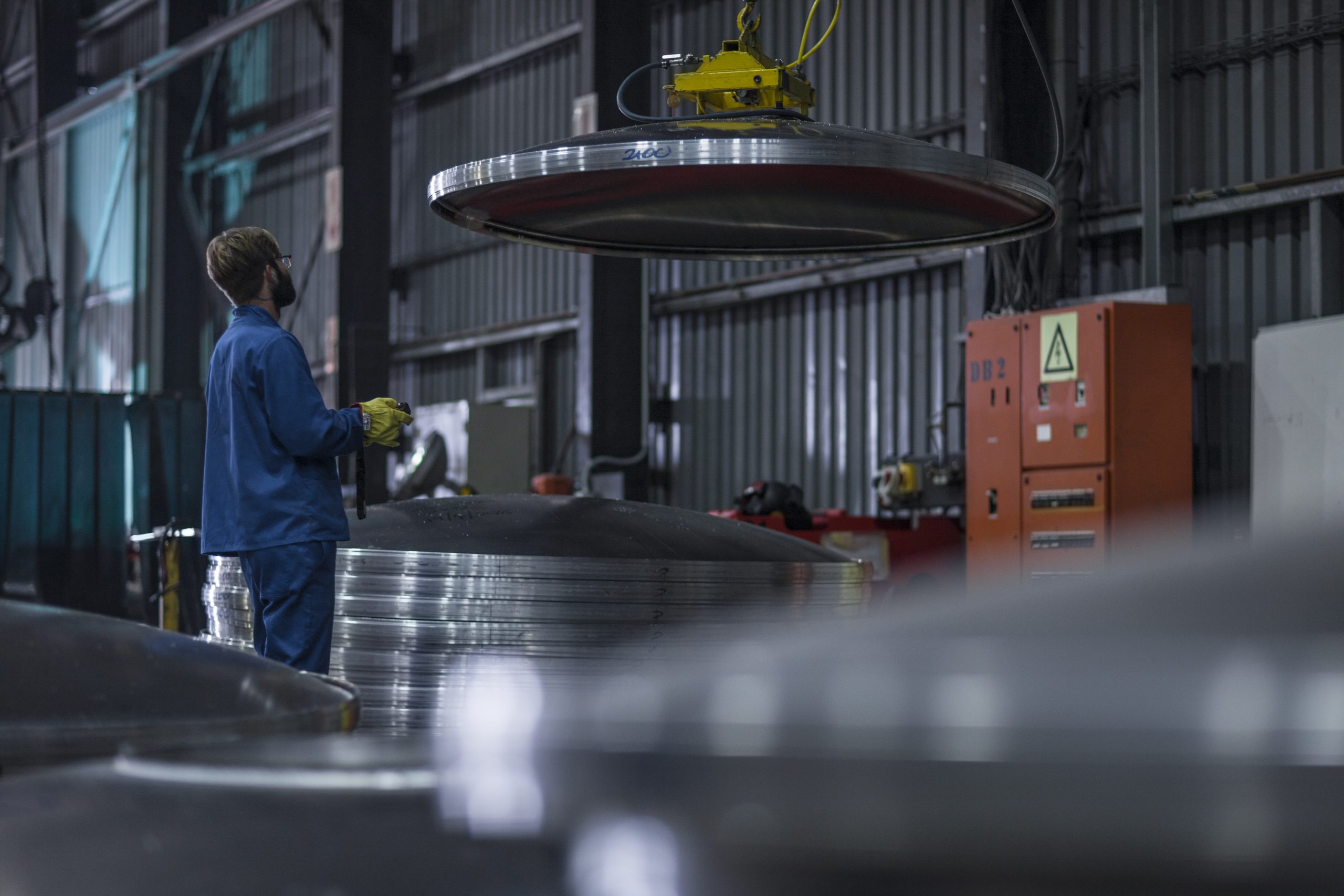
Reducing Waste and Cutting Costs with Metal Spinning
One of the most significant cost advantages of metal spinning is its ability to minimise material waste. Compared to subtractive manufacturing techniques such as machining, which removes material to achieve the final shape, metal spinning works by reshaping metal without any significant loss. This approach reduces material costs and makes the process more environmentally sustainable.
For large-scale production, even a tiny reduction in material waste per unit can result in substantial savings over time. Additionally, because metal spinning does not require the extensive cutting or welding associated with other manufacturing techniques, manufacturers can lower scrap disposal costs and post-production refinishing costs.
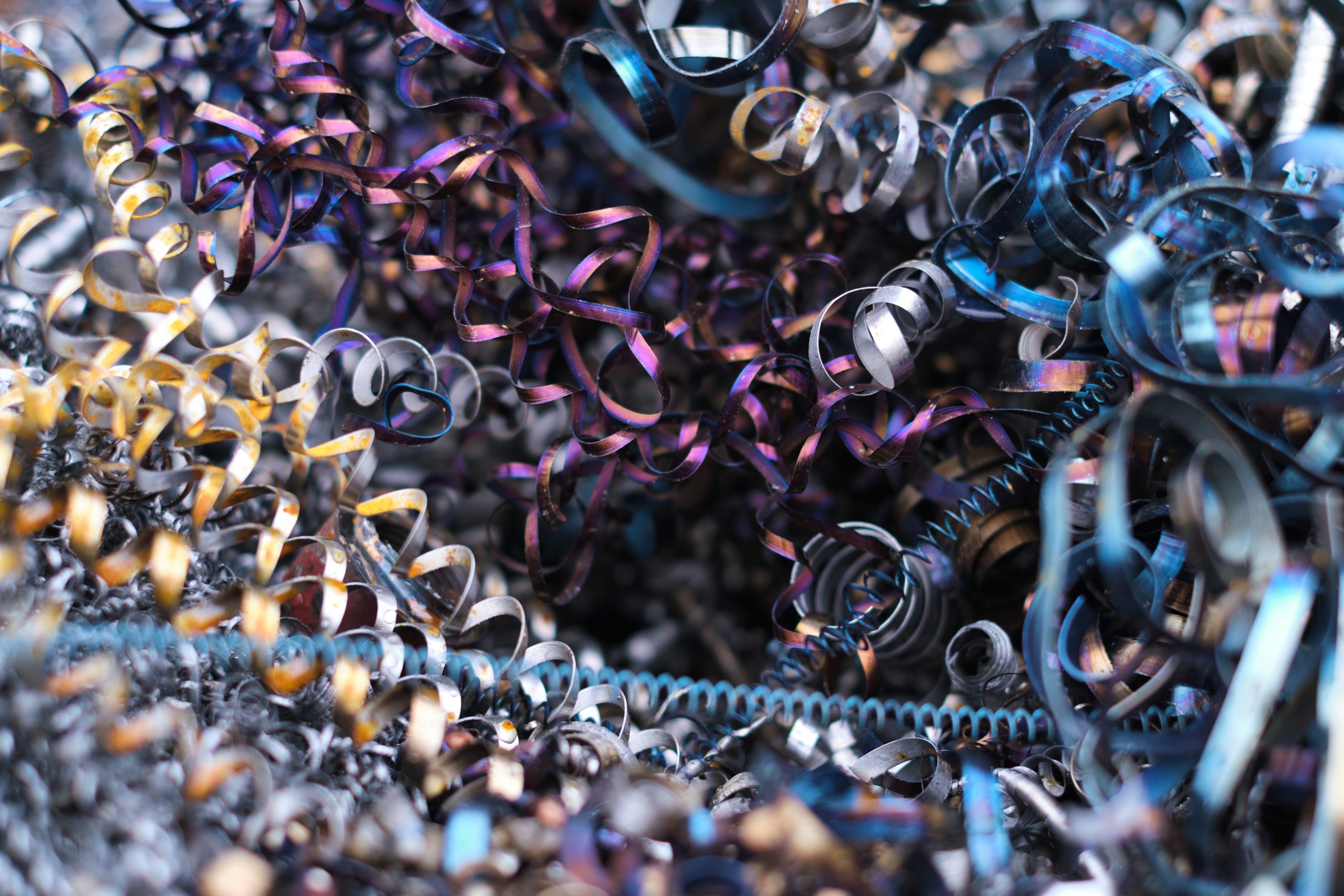
How Metal Spinning Lowers Tooling Costs
Metal stamping and die casting require costly tooling, which can be prohibitive for manufacturers looking to scale production efficiently. Stamping, for instance, involves the creation of heavy-duty dies that can each cost thousands of pounds and require weeks or months to manufacture. Additionally, modifying these dies for design changes can be an expensive and time-consuming process.
In contrast, metal spinning requires minimal tooling investment. The primary tool – a mandrel – is far more straightforward and cost-effective than the dies used in stamping or casting. Furthermore, design modifications can be made with relative ease, making metal spinning an ideal choice for industries that require flexibility in production or frequent design updates.
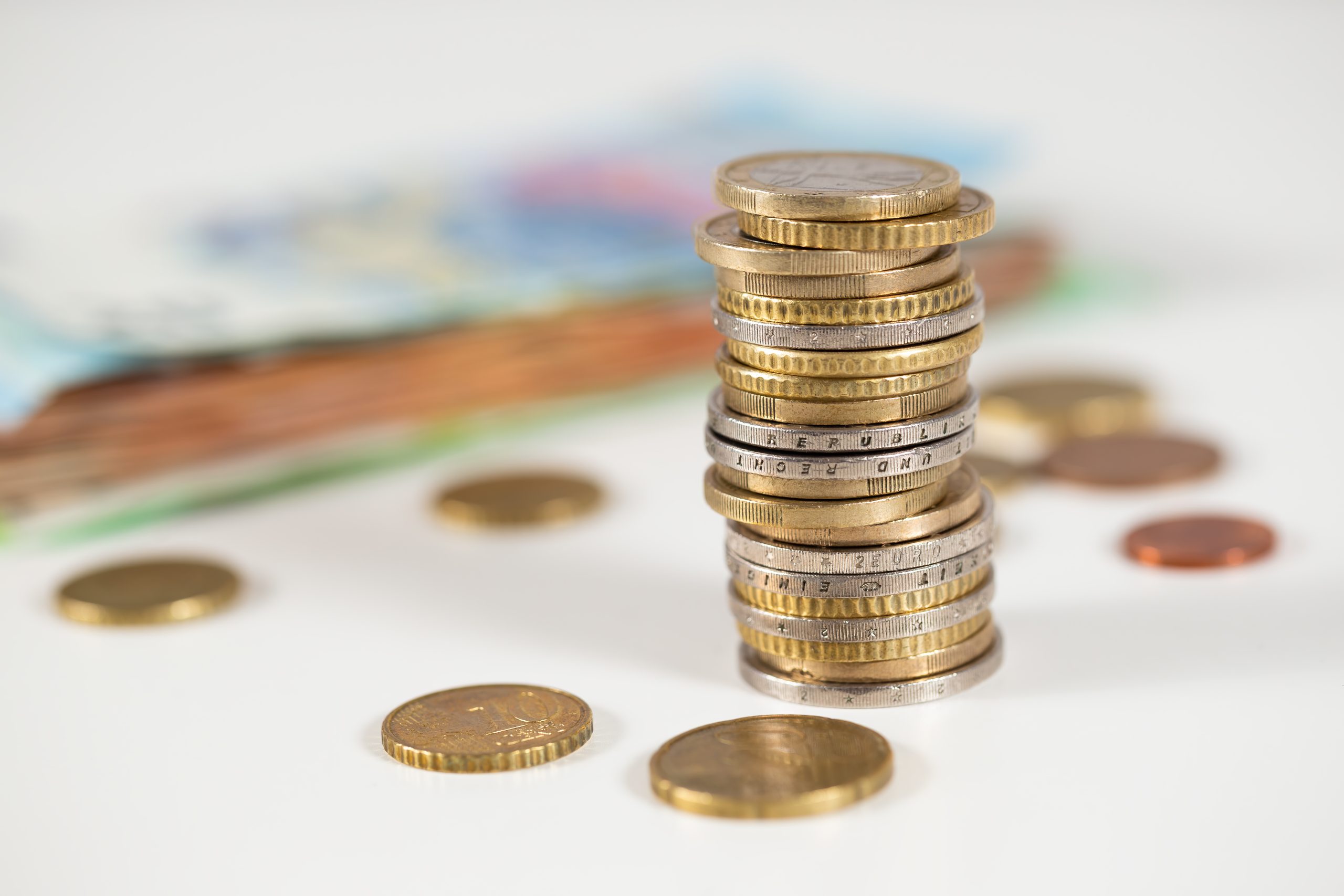
Scaling Up with Metal Spinning: Speed and Efficiency
Speed and efficiency are crucial factors when evaluating the cost-effectiveness of any manufacturing process. Thanks to advancements in CNC (computer numerical control) technology, metal spinning has evolved from a manual art into an automated process that supports both small-batch and large-scale production with remarkable efficiency.
CNC metal spinning allows for rapid production cycles with repeatable precision. This automation reduces labour costs and increases throughput, making it an attractive option for manufacturers needing high volumes of metal components with tight tolerances.
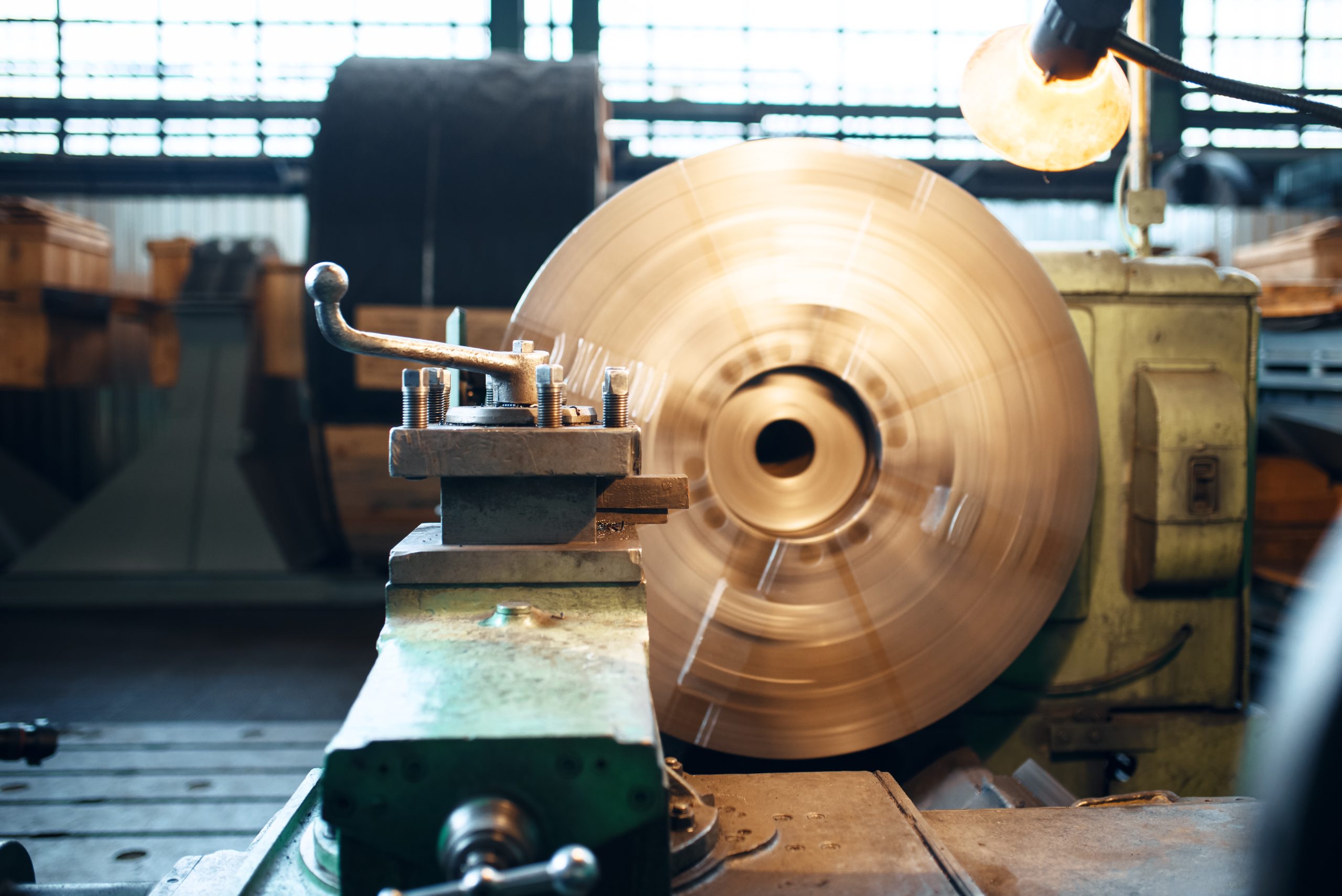
The Versatility of Metal Spinning: Fewer Steps, Greater Savings
Another way metal spinning enhances cost-effectiveness is by reducing the need for additional manufacturing processes. Unlike traditional fabrication techniques that may require multiple steps, such as welding, cutting, and secondary machining, metal spinning can often produce the final shape in a single operation. This one-pass capability eliminates the need for multiple machines and operators, further lowering production costs.
Metal spinning is also compatible with a wide range of metals, including aluminium, stainless steel, copper, and brass, allowing manufacturers to choose the most cost-effective materials suited to their specific applications. This versatility ensures that metal spinning can meet the needs of diverse industries while keeping costs under control.
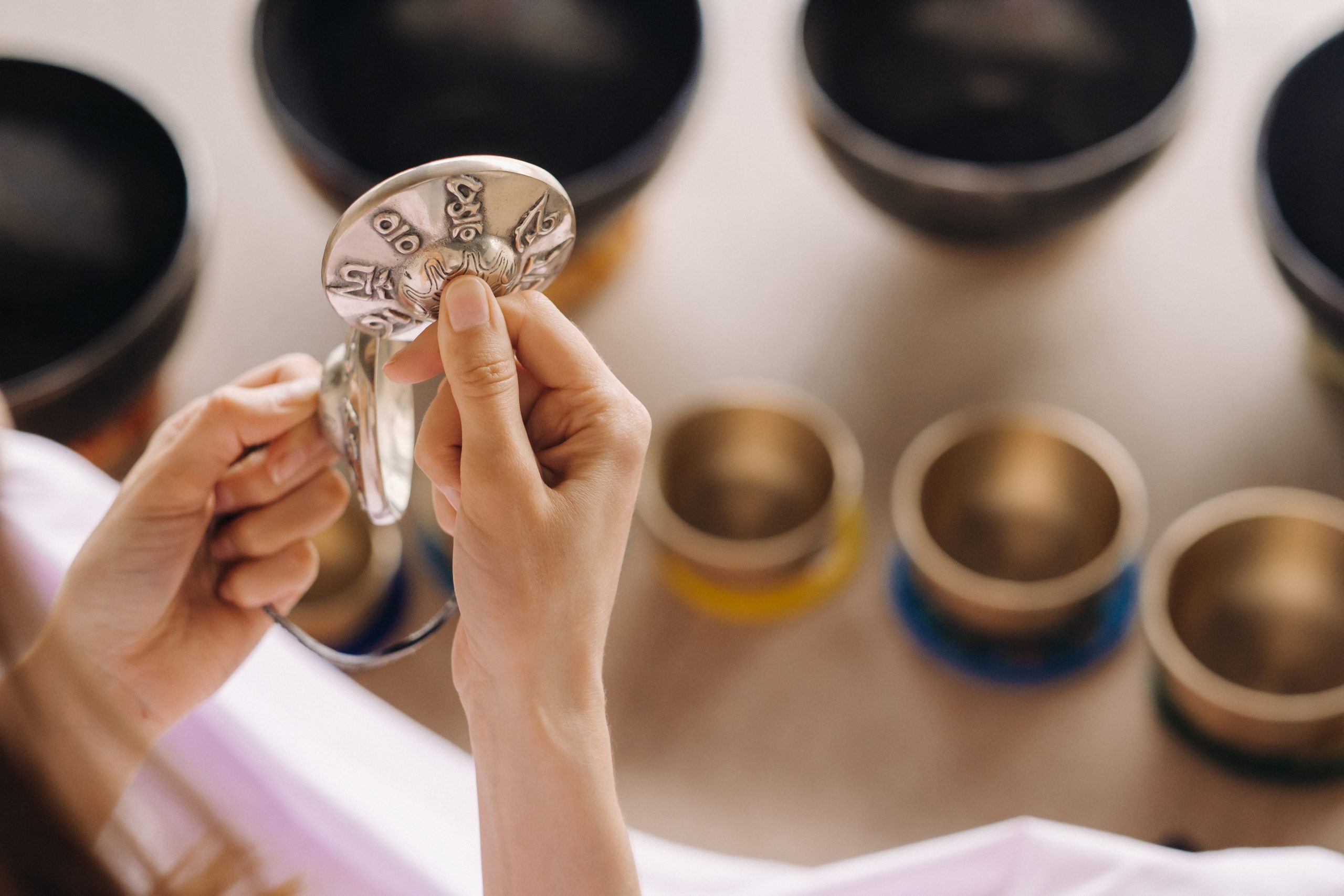
Long-Term Cost Benefits: Durability and Low Maintenance
Products manufactured using metal spinning are often stronger and more durable than those produced using alternative methods. The spinning process aligns with the grain structure of the metal, enhancing its mechanical properties and improving resistance to stress and fatigue. This inherent strength allows the production of thinner yet more resilient components, reducing material usage while maintaining structural integrity.
From a cost perspective, this means fewer component failures and lower maintenance costs over time. Manufacturers that rely on metal spinning benefit from durable, high-performance parts that contribute to long-term operational savings, particularly in industries where product reliability is critical.
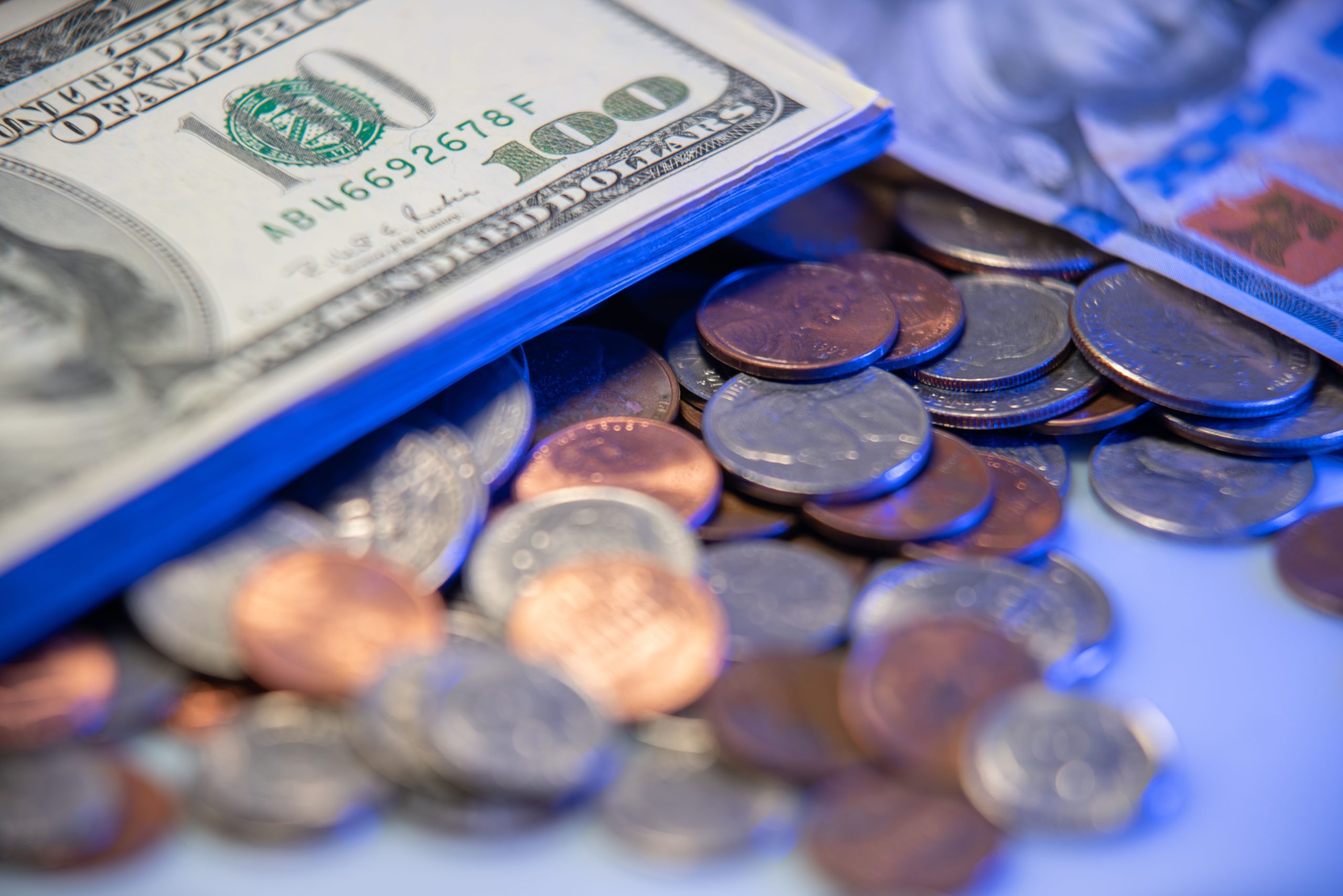
Metal Spinning for Prototyping and Product Development
For manufacturers developing new products, metal spinning offers a very cost-effective route to prototype and refine designs before committing to full-scale production. Stamping and casting both require expensive upfront tooling, whereas metal spinning allows for quick and inexpensive modifications. This agility makes it easier to perfect a design before scaling up production, reducing the risk of costly errors and rework later in the process.
In industries such as aerospace and defence, where component precision and performance are non-negotiable, metal spinning enables the required iterative design adjustments – without breaking the budget. This flexibility ensures manufacturers can efficiently develop and test new products while maintaining cost control.
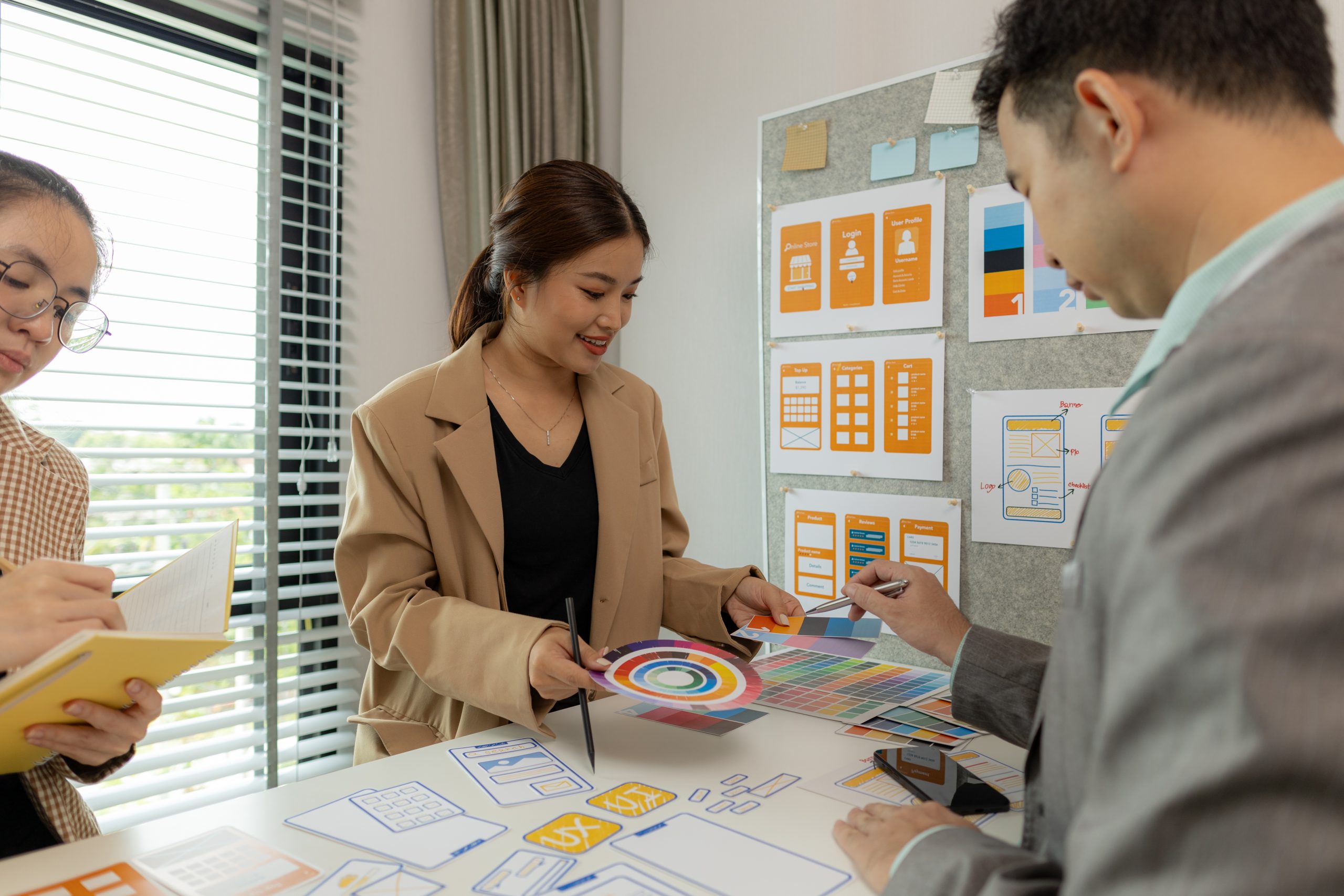
Metal Spinning – the Best Choice for Large-Scale Manufacturing
Concerning large-scale metal component manufacturing, metal spinning offers unparalleled cost advantages. This method delivers a highly efficient and economical metal-forming solution by reducing material waste, minimising tooling costs, increasing production speed, and eliminating unnecessary processing steps.
With the added benefits of durability, scalability, and flexibility, it is clear why metal spinning is a preferred choice for manufacturers looking to balance quality with cost-effectiveness. Whether producing thousands of units or custom-designed components, metal spinning provides a competitive edge in today’s fast-paced manufacturing environment.
Tanfield Metal Spinners offers industry-leading expertise and cutting-edge CNC capabilities for businesses seeking a high-quality, cost-effective solution for metal component production.
Contact us today to discover how our metal spinning services can help you achieve cost savings without compromising on precision and performance.